Health & Safety Advice
-
-
-
-
-
All of our tools are serviced and thoroughly checked before and after hire to ensure the quality and safety of our tools is maintained. Safety is paramount to everything we do at Litchard Tool Hire.
We are committed to providing a safe and secure environment for our staff and our customers. We stock a wide range of PPE at the shop such as gloves, safety glasses, dust masks etc.
Hand Arm Vibration Syndrome (HAVS) has emerged as a major concern for those who work with high vibration equipment. The applicable tools are labelled to indicate the vibration risk to the user. The symbols have the following meaning and recommendations:
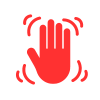
High Vibration Risk
Over 10 m/s2. These pose a high threat of injury, even when used for a short period in a day. Specific assessment is required.
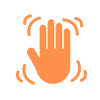
Medium Vibration Risk
Between 5 - 10 m/s2. These tools can be used for a maximum of 2 hours daily. Products on the lower end of this range may be used for longer periods when justified by a risk assessment.
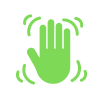
Low Vibration Risk
0 - 5 m/s2. These tools can be used regularly throughout an 8 hour shift with minimal risk of injury.
A summary of the requirements, according the The Working at Height Regulations 2005, are as following:
1. Risk Assessment - Before undertaking any work at height, a thorough risk assessment must be conducted. This assessment should identify potential hazards, evaluate the risks, and determine the most suitable control measures to prevent falls.
2. Hierarchy of Control Measures - The regulations emphasize the hierarchy of control measures, outlining that work at height should be avoided where possible. If this is not feasible, collective protective measures (such as guardrails, safety nets) should be used before resorting to personal protective equipment (such as harnesses).
3. Competence and Training - Individuals involved in work at height must be competent and adequately trained for the tasks they are undertaking. This includes training on the proper use of equipment, understanding of risk assessments, and familiarity with safety procedures.
4. Selection of Appropriate Equipment - The regulations require the careful selection of appropriate equipment for working at height. This includes ensuring that equipment is suitable for the specific task, regularly inspected, properly maintained, and complies with relevant safety standards.
5. Inspection and Maintenance - Regular inspection and maintenance of equipment are essential. The regulations mandate that all work at height equipment, including ladders, scaffolding, and personal protective equipment, must be inspected at regular intervals to ensure it remains in safe working condition.
Acknowledging the potential for both temporary and permanent hearing damage resulting from exposure to noise is paramount. Addressing this potential threat requires ensuring that individuals operating in or around noisy environments are equipped with the necessary Personal Protective Equipment (PPE).
Adhering to the mandates of The Control of Noise at Work Regulations 2005, a compulsory noise assessment is required when the noise surpasses 80 dB(A).
The generation of dust is inevitable when using power tools, and it presents a distinct health and safety hazard. Dust exposure carries risks such as respiratory issues and irritation to the eyes and skin, emphasising the importance of addressing and reducing these risks.
In addition to the obvious requirement for PPE, such as goggles and dust masks, we highly recommend the use of dust extraction equipment when using power tools to further reduce the risks.
All of our tools are serviced and thoroughly checked before and after hire to ensure the quality and safety of our tools is maintained. Safety is paramount to everything we do at Litchard Tool Hire.
We are committed to providing a safe and secure environment for our staff and our customers. We stock a wide range of PPE at the shop such as gloves, safety glasses, dust masks etc.
Hand Arm Vibration Syndrome (HAVS) has emerged as a major concern for those who work with high vibration equipment. The applicable tools are labelled to indicate the vibration risk to the user. The symbols have the following meaning and recommendations:
High Vibration Risk
Over 10 m/s2. These pose a high threat of injury, even when used for a short period in a day. Specific assessment is required.
Medium Vibration Risk
Between 5 - 10 m/s2. These tools can be used for a maximum of 2 hours daily. Products on the lower end of this range may be used for longer periods when justified by a risk assessment.
Low Vibration Risk
0 - 5 m/s2. These tools can be used regularly throughout an 8 hour shift with minimal risk of injury.
A summary of the requirements, according the The Working at Height Regulations 2005, are as following:
1. Risk Assessment - Before undertaking any work at height, a thorough risk assessment must be conducted. This assessment should identify potential hazards, evaluate the risks, and determine the most suitable control measures to prevent falls.
2. Hierarchy of Control Measures - The regulations emphasize the hierarchy of control measures, outlining that work at height should be avoided where possible. If this is not feasible, collective protective measures (such as guardrails, safety nets) should be used before resorting to personal protective equipment (such as harnesses).
3. Competence and Training - Individuals involved in work at height must be competent and adequately trained for the tasks they are undertaking. This includes training on the proper use of equipment, understanding of risk assessments, and familiarity with safety procedures.
4. Selection of Appropriate Equipment - The regulations require the careful selection of appropriate equipment for working at height. This includes ensuring that equipment is suitable for the specific task, regularly inspected, properly maintained, and complies with relevant safety standards.
5. Inspection and Maintenance - Regular inspection and maintenance of equipment are essential. The regulations mandate that all work at height equipment, including ladders, scaffolding, and personal protective equipment, must be inspected at regular intervals to ensure it remains in safe working condition.
Acknowledging the potential for both temporary and permanent hearing damage resulting from exposure to noise is paramount. Addressing this potential threat requires ensuring that individuals operating in or around noisy environments are equipped with the necessary Personal Protective Equipment (PPE).
Adhering to the mandates of The Control of Noise at Work Regulations 2005, a compulsory noise assessment is required when the noise surpasses 80 dB(A).
The generation of dust is inevitable when using power tools, and it presents a distinct health and safety hazard. Dust exposure carries risks such as respiratory issues and irritation to the eyes and skin, emphasising the importance of addressing and reducing these risks.
In addition to the obvious requirement for PPE, such as goggles and dust masks, we highly recommend the use of dust extraction equipment when using power tools to further reduce the risks.